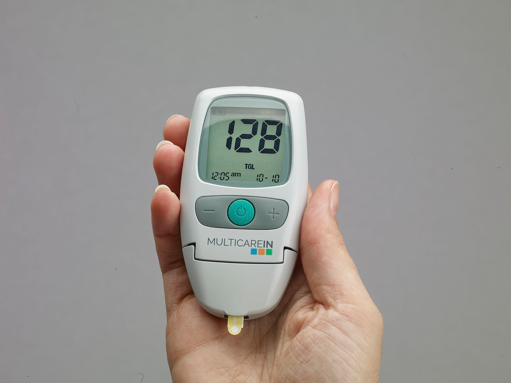
The production of medical devices has been completely transformed by laser processing. It offers accurate, effective, and flexible solutions for a variety of uses. Lasers provide unparalleled precision in an industry where accuracy is crucial. This enables manufacturers to create complex designs and adhere to strict regulatory requirements.
Laser technology is becoming increasingly essential as the medical device sector develops to fulfill the demands for efficiency, quality, and innovation.
Use of Laser Technology in Medical Device Manufacturing
Laser processing can accomplish tasks with a precision that older technologies cannot equal. Therefore, it has become an indispensable tool in the manufacturing of medical equipment.
According to Fortune Business Insights, the size of the worldwide medical laser market was estimated to be $5.17 billion in 2023. It is anticipated that by 2032, the market will have more than doubled from $5.47 billion in 2024 to $11.26 billion. This indicates a 9.4% CAGR over the duration of the prediction.
Numerous procedures, including cutting, welding, drilling, labeling, and surface modification, are carried out with this technology. In order to guarantee that medical devices fulfill the essential requirements for both performance and safety, each of these applications is essential.
Precision Cutting and Micromachining
Among the most used laser processing techniques in the production of medical devices are precision cutting and micromachining. Lasers are perfect for creating components with intricate geometries because of their remarkable precision in cutting and shaping materials.
The accuracy of laser cutting guarantees that every component fits precisely in the creation of various equipment. This helps lower the possibility of malfunction or failure.
An article from Medical Product Outsourcing states that miniaturization and the highest precision are the top goals in the minds of leaders. A sales and marketing head of a global medical device manufacturing firm said that precision is one of its most lucrative features. For instance, laser texturing is being used more frequently to strengthen bindings, particularly those between metal and plastic.
Micro-holes, grooves, and channels, small features that are difficult to create on medical devices, can be made by micromachining. In situations like medication delivery systems or microfluidic devices, these characteristics are frequently essential to the device’s operation.
These characteristics can be produced by lasers precisely, guaranteeing that the gadgets function as intended. Furthermore, laser micromachining provides a repeatability that is essential for mass manufacturing.
As stated by Novanta Photonics, this precision is also one of the reasons why lasers are being used across multiple medical aspects. From microscopy and cellular imaging to surgeries and cosmetics, laser solutions are offering both quality and control. This has helped healthcare organizations offer enhanced experiences to patients who have been treated using these systems.
Laser Welding for Medical Devices
Another essential use in the production of medical devices is laser welding. The integrity of delicate components must be preserved while joining materials with this technique. Laser processing solutions can join them precisely and with little heat input.
Laser welding provides an effective approach to welding robust, long-lasting connections without sacrificing the material’s qualities in medical equipment, where dependability is critical.
For example, laser welding is utilized to seal the pacemaker’s case during manufacture, guaranteeing that it stays moisture-free and hermetically sealed. This is essential for both patient safety and the long-term performance of the device.
Manufacturers are also able to fuse disparate materials that are frequently utilized in medical equipment thanks to the accuracy of laser welding. This feature creates new opportunities for the functioning and design of devices, facilitating the creation of increasingly complex and advanced goods.
Surface Modification and Texturing
Surface modification and texturing techniques are significant in the production of medical devices. That’s because they have an immediate effect on the functionality, durability, and biocompatibility of the product. A flexible method for precisely altering surfaces, laser processing, enables producers to customize the surface’s characteristics to fulfill demands.
Surface texturing, for instance, can enhance osseointegration, the process by which an implant fuses with the surrounding bone tissue in implanted devices. Improved clinical results can be achieved by using lasers to produce micro- and nano-scale textures that encourage cell adhesion and proliferation.
Furthermore, medical gadgets’ corrosion and wear resistance can be improved by laser surface modification, prolonging their useful lives and guaranteeing their dependability.
Surface can also be pre-treated with the help of clean lasers. There are many devices that may require pre-treatment, especially metal surfaces, before coating. Lasers can help remove residue, oil, or grease from the metal surfaces to improve its coating adhesion. This can help produce parts that are corrosion-resistant.
Frequently Asked Questions
What are some advantages of using lasers in manufacturing?
Benefits of laser processing include faster processing times, higher-quality surface finishes, more adaptability, non-contact processing, smaller heat-affected zones, and cost-effectiveness. Manufacturers may make use of these advantages to produce precisely made, durable goods.
What is the role of laser in additive manufacturing?
Using a 3D computer-aided design (CAD) model, a laser beam melts and solidifies material layer by layer in laser additive manufacturing (LAM). Even in complicated components, the laser’s precision spatial control makes it possible to create both fine and bulk features. LAM is utilized for quick prototyping, high-cost part repair, and aerospace, astronautical, and aeronautical applications.
What is laser welding used for?
Numerous metals, such as molybdenum, titanium, Inconel, nickel, and stainless steel, may be joined together by laser welding. Shiny materials like copper and aluminum may also be welded using a laser.
Laser processing offers the highest levels of accuracy, effectiveness, and adaptability. Therefore, it has become an essential instrument in the production of medical devices. Its uses include welding, surface modification, micromachining, precision cutting, and marking, all essential processes for creating high-grade medical equipment. The future of medical device production is expected to be significantly shaped by the advancement of laser technology.
Facebook Comments